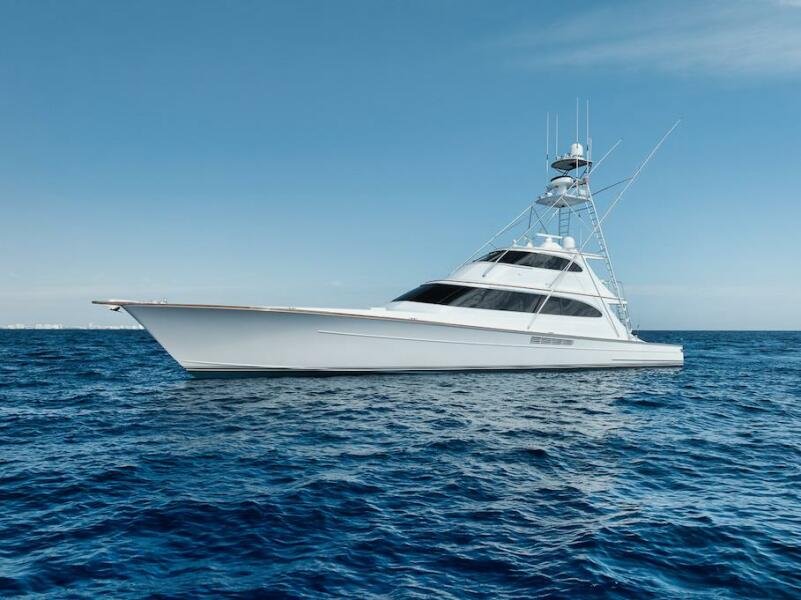
GS-Saltwater Fouling Release and Speed Coating.
For vessels that reside in saltwater.
Our GS-Saltwater Fouling Release Speed Coat is revolutionary and self Cleaning! It will prevent the adhesion of barnacles and undergrowth on bottoms that reside in the saltwater (If adhered to our maintenance protocol) and decreasing friction while underway. Benefits will be decreasing fuel consumption at cruising speed and achieve better speed at lower RPM’s, Easy cleaning and long lasting. It will also outlast other bottom coats as it contains no biocides.
Today’s biocide/ablative coatings are lucky to get 6 months before needing constant maintenance and recoating due to the limitations placed by the E.P.A. This is where we shine! If you keep your boat in the Saltwater, you need/want GatorGlide GS! We recommend the boat be underway very 3 to 4 weeks for self-cleaning. If that is not an option, then wiping the bottom with a microfiber towel will have the same cleaning effect. We are comparatively priced for the start and will outlast the rest. Depending on your bottom/substate the application will vary. As always GatorGlide has a vested interest in your outcome/success. We strongly believe your success is our success which makes us a team! Never hesitate to reach out to me for guidance with your specific project.
For all prior painted or oxidized substrates, we highly recommend first using our GatorBond Epoxy primer first to ensure max adhesion. It also contains corrosion protection on steel, the topcoat does not.
For aluminum and steel bare metal: 30 - 60 grit sandpaper for initial cutting followed by 80 - 120 grit sandpaper for a smoother surface. Next apply the GatorBond Primer to the TDS specifications. You are then ready for the GS Saltwater release.
Fiberglass: 120-220 (Depend on the look you’d like to achieve) grit sand prior to GS Saltwater release. However, to warranty the product outcome on all substrates you will need to use GatorBond as well as if forms a moisture barrier coat the GS does not provide. Gelcoat inherently holds moisture unless it is dried out thoroughly.
We have had great success with GatorGlide products on top of new and old ablatives coatings but cannot warrantee due to conditions beyond our control. This is where common sense and experience of the user comes in.
GS is a Two-part aliphatic urethane and cures by polymerization of the two components (polyol and isocyanate). However, when applied over moisture, bubbles can form on the backside of the urethane film This can occur due to the isocyanate component of the urethane formulation reacts with moisture. As with the MCU reaction discussed earlier, CO2 gas is formed. The gas is typically trapped in the lower layers of the urethane coating film and also at the interface of any previously applied coating where the moisture was present. Again, the pressure created by the gas formation causes bubbles to form. One difference with this formation process is that the bubbles can be very fine and are not always visible to the unaided eye. When viewed microscopically in a cross section, the fine bubbles often have a foam-like appearance. For this reason, this phenomenon is typically referred to as “foaming.” In the case of bubbles with MCU and aliphatic urethane formulations, the outgassing that occurs between layers can disrupt adhesion. Typically, other forms of bubbling have little to no adverse effect on coating adhesion, unless very intense and concentrated.
We have tested GS over new Ablative (un-named) bottom coating with great success. It stands to reason that if you have recoated with an ablative bottom coating then topcoat with our GS it should preserve the undercoat, seal in the biocides (for later if need be) and the GS takes over. If you were to damage just the GS leaving the ablative coating, that area would then be reliant on the ablative coating until a GS repair was done. GS has been in the water for three years without fail! How long will it protect your investment?